Optimisation Specialists
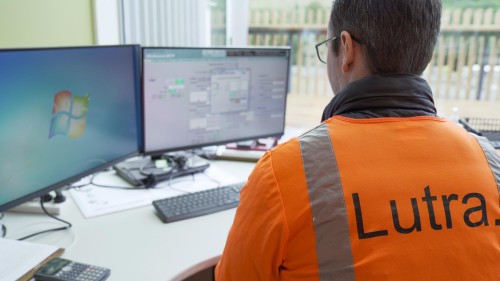
Lutra are Optimisation specialists
Our team of experienced engineers can look at your treatment data, samples, SCADA trends and more and find ways to optimise any processes that may be either under-performing or costing too much.
Our deep knowledge of water and wastewater processes mean we can find ways to optimise that others can't. Lutra have a proven track record at delivering optimisations with meaningful material/cost savings while delivering the same or even better levels of treatment.
Optimisation - Savings and Gains
Save Money
Optimisation often means reduced chemical or electricity usage resulting in direct operational savings.
Increased Production
Some optimisation can lead to longer runtimes or higher loading rates, increasing production without adding new equipment leading to indirect operational savings or deferring capital investments.
Better Treatment
Improved water quality or treatment reliability are other possible outcomes from process optimisation.
Less Environmental Impact
Optimisation can reduce carbon footprint, green house gas emissions and reduce residual pollutants or chemicals being introduced to the environment.
Optimisation Services
Our engineers are experienced in optimising a wide range of processes including:
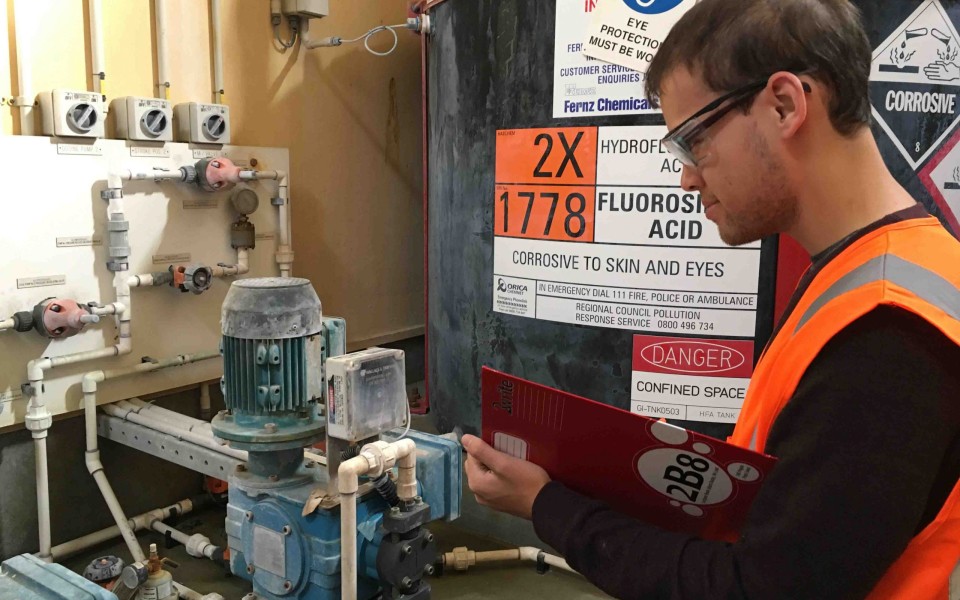
Chemical Systems
Chemical dosing systems in both water and wastewater treatment are often prime for optimisation, as they result in direct savings. Dose rates are often overly cautious, or simply not checked against water conditions regularly enough, especially when you are reaching your performance/compliance targets. But the savings are not to be underestimated, with hundreds of thousands of dollars per year possible. Lutra can dive into your data and trends, perform direct onsite testing and find the most efficient dose rates for all of your chemicals.
CO2 Usage - Potential Reductions of $700,000/year across 2 Wellington Water Treatment Plants.
Coagulant Usage - Proven Reductions of $200,000/year at a surface water WTP sized at 5.8 MLD.
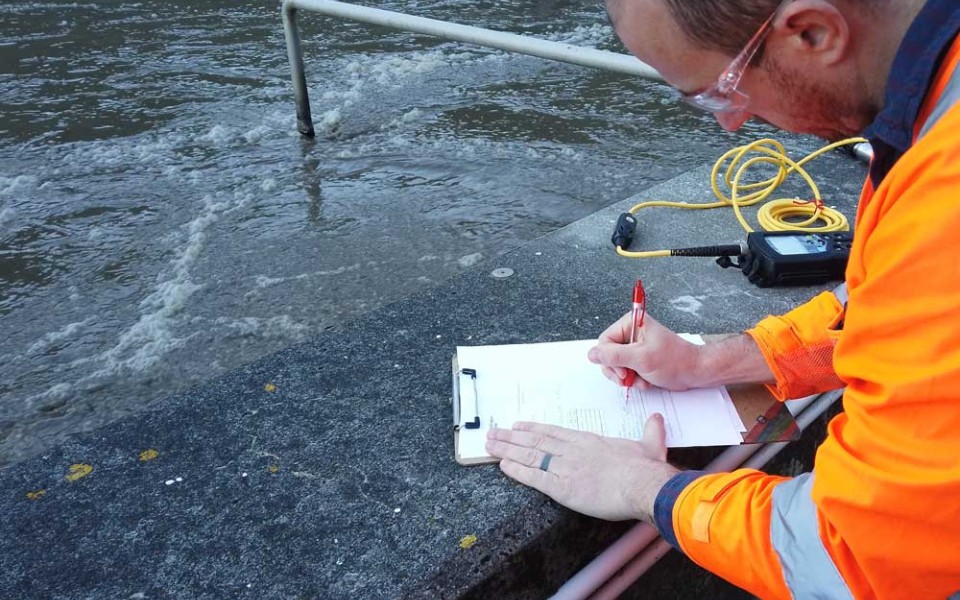
Aeration
Aeration at wastewater treatment plants is often one of the biggest power drains on a community, costing a lot of money and increasing carbon footprint. Trimming the power usage of aerators even by as little as 10% can lead to significant savings without affecting performance.
Lutra's wastewater engineers can looks at your process, specific equipment, samples and performance data to work out the most efficient rate at which to run your aeration systems, saving you power costs and helping to protect the environment. The approach can be as simple as implementing DO control or creating a dynamic DO setpoint based on bioreactor conditions and pollutant concentrations.
Possible power reduction of between 10-25% Per Year.
Running blowers less will also extend their service life saving even more long term.
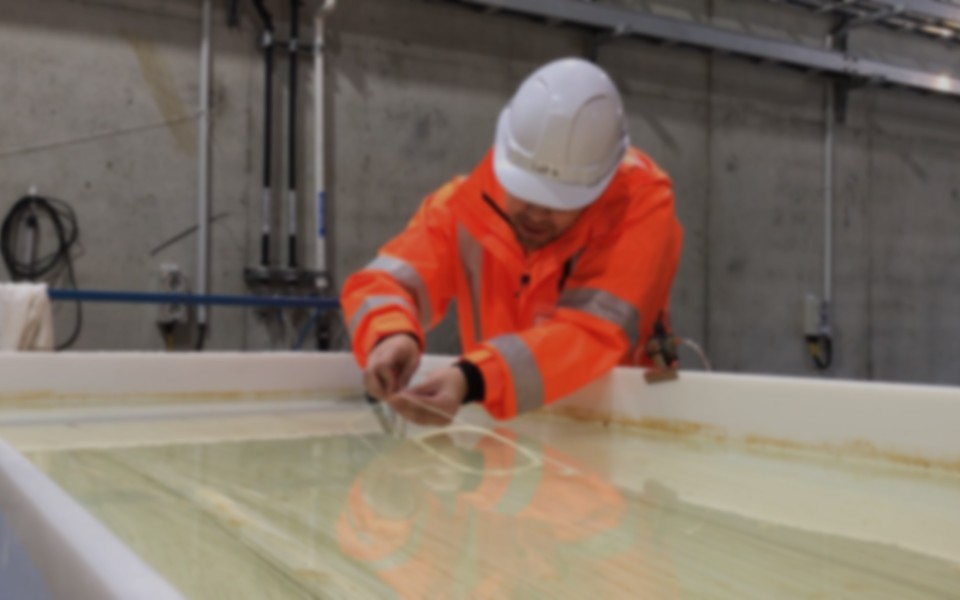
Plant Production Performance
Are your filters or membranes running as efficiently as possible? By optimising filter backwash or CIP frequency, backwash rates, etc., you can often improve the performance of the filters or extend their lifetime. This can be done to different degrees on all backwashable or chemically cleaned filters, from gravity to polymeric membranes. Lutra have experience with all kinds of media filtration systems and know how to get the best out of them.
By looking at data, trends and water samples and testing Lutra can find the best-balanced backwash frequency for your system which can save power and water or due to increased runtime between backwashes actually increase output.
Can increase treatment capacity without requiring new equipment or processes.
Possible increase in media/membrane life.
Case Studies
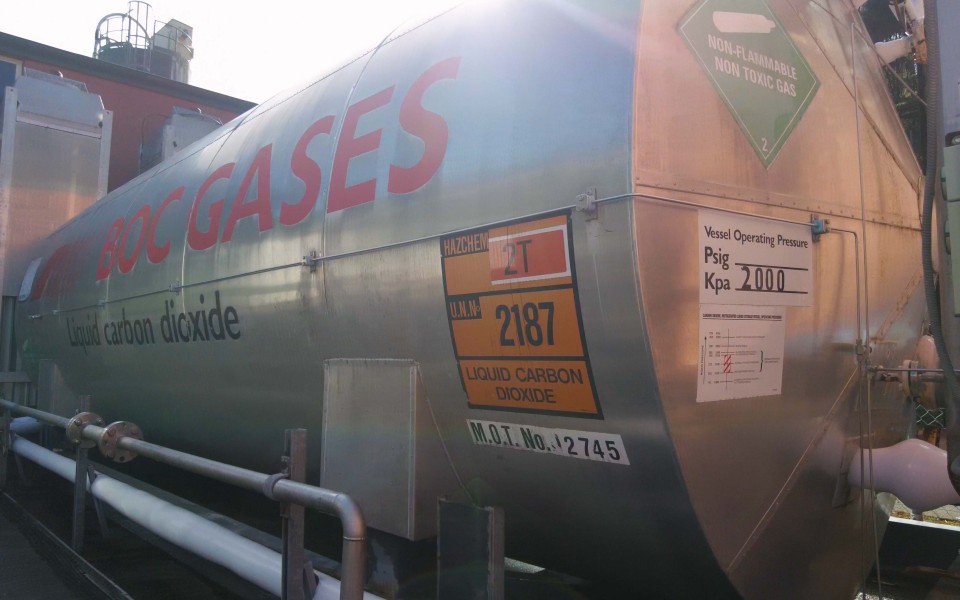
Wellington Water CO2 Optimisation
New Zealand experienced a CO2 shortage in 2023 due to industrial production reductions and supply chain issues. CO2 is used across several Wellington Water plants to adjust pH and add alkalinity. The increased cost and scarcity of CO2 prompted Wellington Water to engage Lutra to optimise CO2 dosing at their Te Marua and Wainuiomata treatment plants.
Estimated Savings $700,000/year.
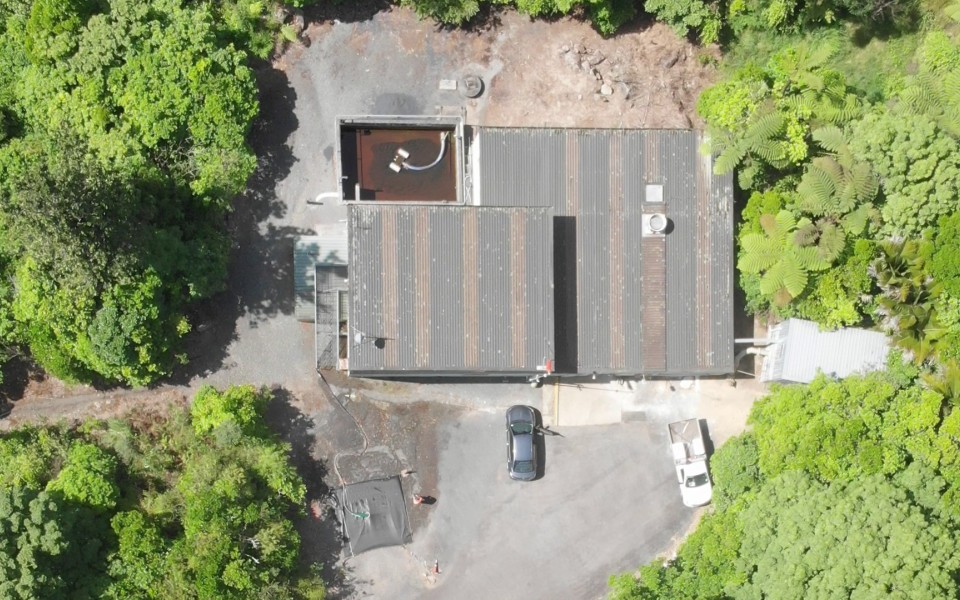
Coagulant Optimisation Municipal WTP
After noticing operational issues at a 5.8MLD surface water treatment plant Lutra was employed to investigate and optimise the chemical dosing. Lutra found that the alum dose rates were higher than necessary, and were able to make adjustments that halved their usage without reducing treatment levels. The reduction in alum had the compounding effect of allowing a reduction in pH adjusted chemicals.
Estimated Savings $200,000/Year
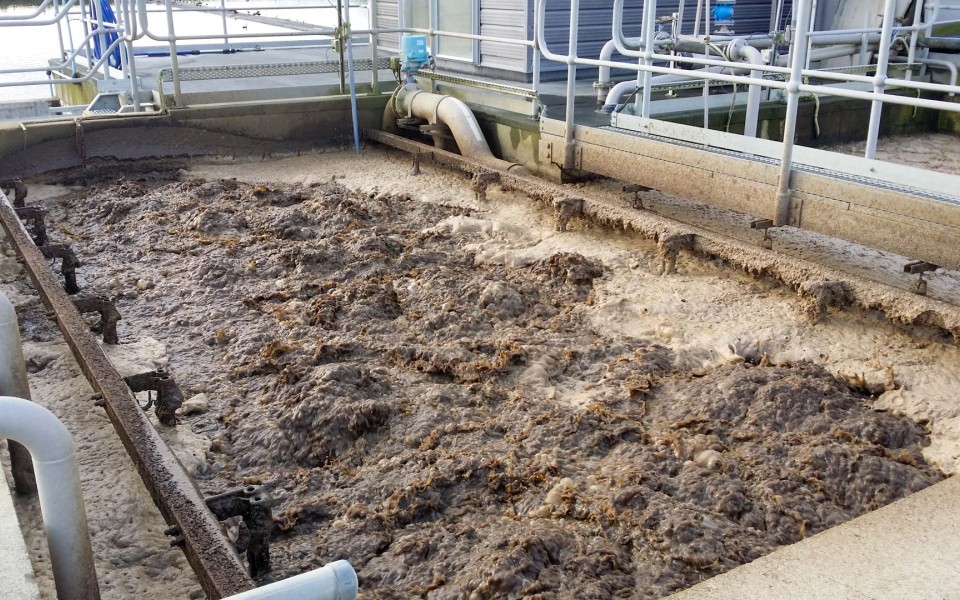
Membrane Bioreactror (MBR) Optimisation
One of Lutra’s clients operates a flat sheet MBR plant to treat 2,000 m3/d. After reviewing the filtration, relaxation, and aeration setpoints, operation, and performance onsite, Lutra’s recommendations were implemented and resulted in 25-30% net flux capacity increase. The capacity increase resulted in more idle time for the MBR, reducing aeration power requirements.
Estimated Savings $15,000/Year
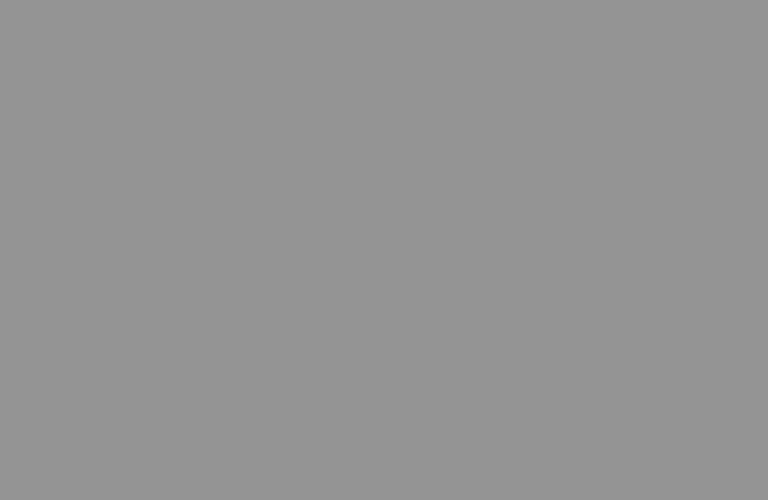
Some of our Optimisation Experts
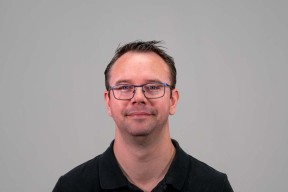
Jonathan Church
Principal Process Engineer
Jonathan is our Principal Process Engineer with over 14 years of experience in the design, commissioning, optimisation and operation of treatment plants.
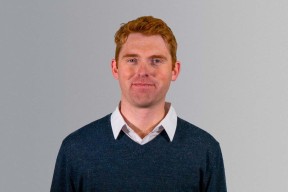
Richard Slight
Water Team Leader
Richard has a wide range of experience in the water industry, from practical site work to operating water plants through to design and project management.
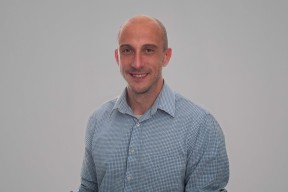
Louis Ortenzio
Chief Engineer
Louis is the Chief Engineer, heading up our Water and Wastewater Process Engineering Teams. With almost 20 years of International experience in design, commissioning, operations, and piloting with a passion for innovation, Louis continues to grow and diversify Lutra's expertise and offerings.
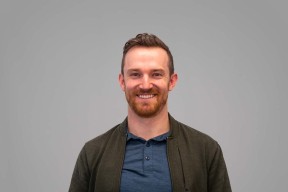
Tim Miskimmin
Wastewater Team Leader
Tim has over 10 years experience as a process engineer, delivering engineering projects and design solutions to safely maintain and improve process plants and now uses this to lead our wastewater team.